What is torque?
Torque is any force, or system of forces, that tends to cause rotation about an axis
How does a torque wrench work?
The wrench gives a clear indication to the operator when the set torque is reached and he can stop applying force.
The three types of indication on Norbar torque wrenches are:
“CLICK”, “SLIP” and “BREAK”
What is required in a torque wrench?
Easy setting of required torque; ability to tighten a variety of fastenings; accuracy of applied torque; repeatability of results; durability. Unique on a Norbar torque wrench, the TimeStrip® gives a visual indication that the wrench is due for re-calibration.
What is the accuracy of a torque wrench?
All Norbar torque wrenches are ± 3% to ± 4% accuracy; all have accuracy within international standards. Norbar has a multi-scale measuring indicator that can adopt to the operator needs: (N-m, k-N, lbf-ft, and lbf-in.)
How often should a wrench be calibrated?
“For the first recalibration, the period of validity starts with the user’s first operation of the torque tool”, ISO 6789 recommends every 5000 cycles or 12 months or once per year, from the user’s first operation and not from the date of manufacture.
View further information on Calibration Periods for Torque Wrenches.
How is accuracy tested?
Using torque measurement equipment in accordance with the relevant Standard. ISO 6789-1:2017 takes 5 readings at a minimum value of the scale, 60% and 100% of full scale – all must be within tolerance. ISO 6789-2:2017, evaluation of tool will require to collect over a hundred readings.
(ISO6789-1:2017) Part 1: Requirements and methods for design conformance testing and quality conformance testing — Minimum requirements for certificates of conformance
(ISO6789-2:2017) Part 2: Requirements for calibration and determination of measurement uncertainty. Learn More about ISO-6789 here.
Why must torque tools be tested?
Torque tools are used to ensure that correct torque values are applied; the continuity of their accuracy of operation must be confirmed periodically.
The importance of keeping your torque tools in peak calibration condition is well established. Many businesses achieve this by using a third party calibration service.
However, how much more convenient would it be to perform calibration checks inhouse? Tools could be checked more frequently, immediately if a problem is suspected, and tools would not need to leave site unnecessarily.
The main reasons that more companies do not perform calibration checks on their own tools are the cost of testers and fears over the complexity of the testing equipment.
Norbar’s ‘TruCheck’ torque screwdriver testers aim to sweep aside these concerns. They are very cost effective being significantly cheaper than most similar products on the market and the basic version of the TruCheck particularly is very simple to use.
Download the Norbar catalog here
Why can’t my torque wrenches cannot be calibrated and complete on the same day?
Based on NATA, our calibration procedure states that every tool that needs to recalibrate must be stabilize to the lab temperature of 20 degrees plus or minus 2 degrees for 8 hours.
What is the friction in the bolted joint?
When a threaded fastener is tightened, the induced tension results in friction under the head of the bolt and in the threads. It is generally accepted that as much as 50% of the applied torque is expended in overcoming friction between the bolt head and the abutting surface and another 30% to 40% is lost to friction in the threads. As little as 10% of the applied torque results in useful work to tension the bolt.
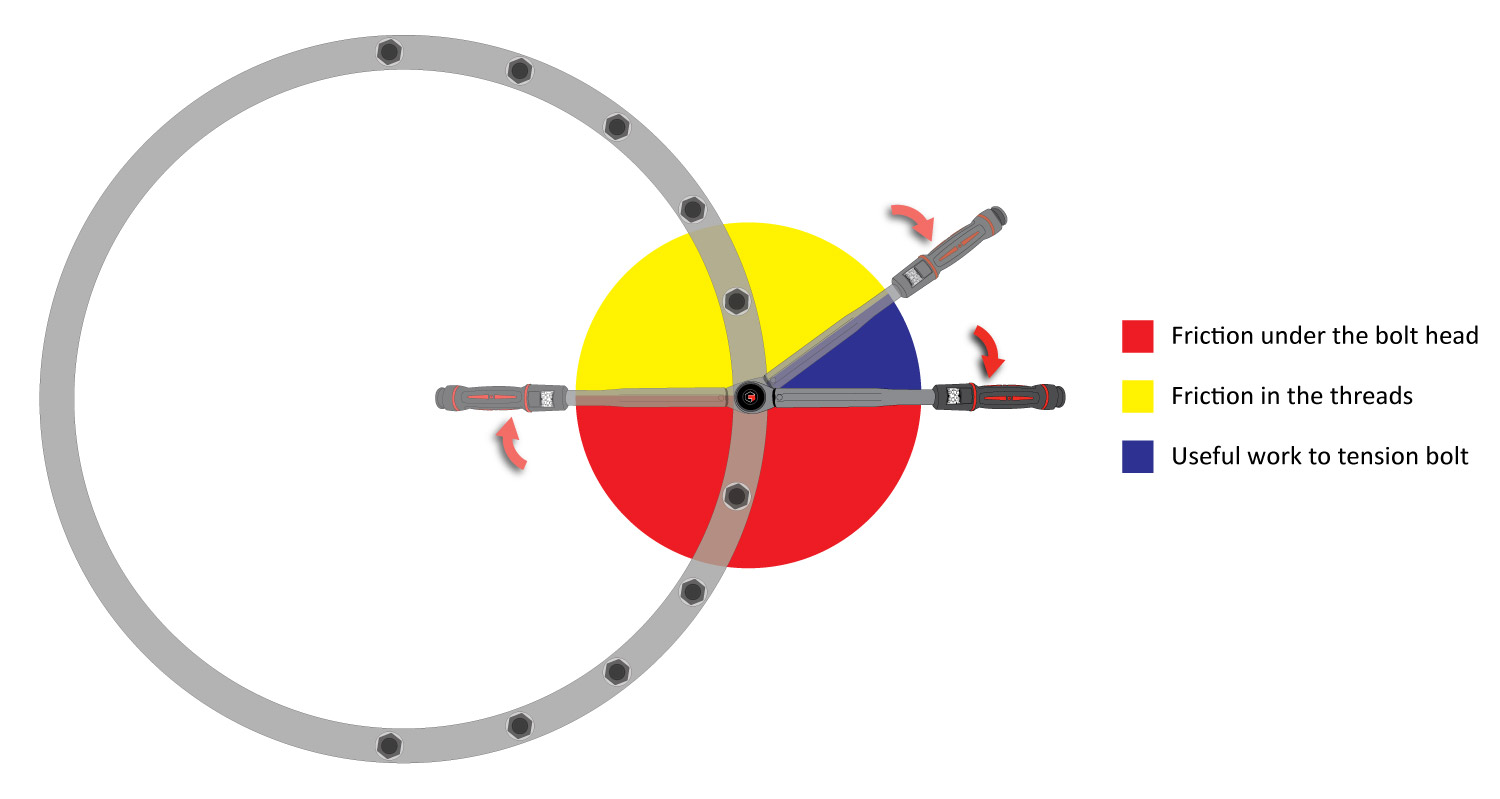
Given that up to 90% of the applied torque will be lost to friction, it follows that any changes in the coefficient of friction resulting from differences in surface finish, surface condition and lubrication can have a dramatic effect on the torque versus tension relationship. Some general points can be made:
Most torque tightened joints do not use washers because their use can result in relative motion between the nut and washer or the washer and joint surface during tightening. This has the effect of changing the friction radius and hence affects the torque-tension relationship. Where a larger bearing face is required then flange nuts or bolts can be used. If washers are to be used, hard washers with a good fit to the shank of the bolt give lower and more consistent friction and are generally to be preferred.
Industry Applications for Norbar Torque Tools:
- Aerospace
- Mining
- Construction
- Oil and Gas
- Power Generation
- Manufacturing and Assembly
- Transportation
Send your inquiries to: