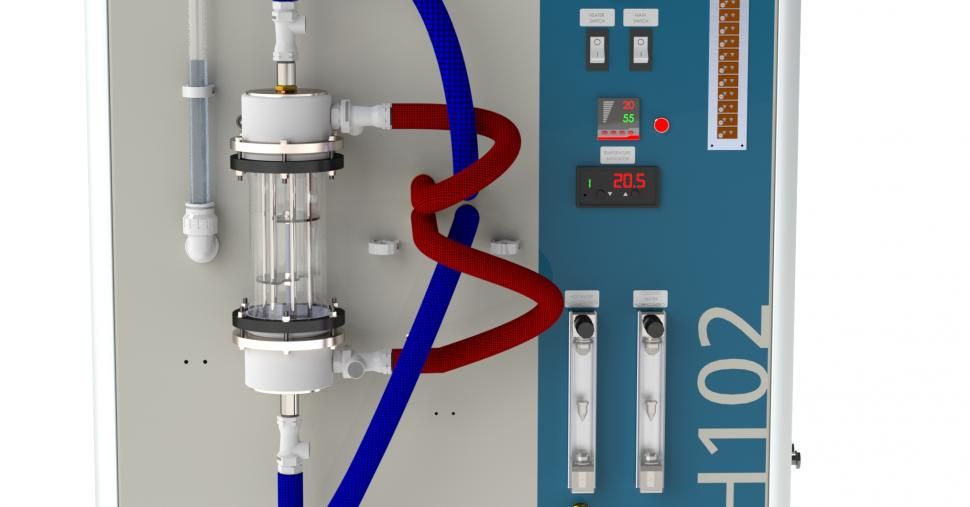
If you read our last blog then you’ll already be aware of the awesome Power of Four. We mentioned the four seasons, four Beatles, four Gospels and much more on the topic of four!
This time we’re here to talk about another awesome foursome – the four main heat exchangers in the PA Hilton product range.
As we note in this previous blog, heat exchange is a fundamental principle of engineering and is so crucial to the way we live, work, and travel that it’s covered in the first year of learning for any engineering student, whatever discipline they go on to pursue.
As a result, much of the thermodynamics equipment produced by PA is geared towards demonstrating heat exchange and the vast range of applications it has in the real world.
All our four core heat exchangers are designed to work with the H102 Heat Exchanger Service Unit. This is a bench-mounted panel with an integral electrical console that provides services for the optional heat exchangers. Hot and cold water is controlled and measured using variable area flowmeters.
Our optional heat exchangers are then connected to the H102 using self-sealing couplings so students can measure variations in temperature as various heat exchange experiments are carried out. An optional computerised data acquisition upgrade can be used to record results on a computer in real time.
Our fab four – which we call H102A to H102D – are designed to showcase the four main methods of heat exchange.
The core four are:
H102A – Concentric Tube Heat Exchanger
Two separate concentric tubes are arranged in parallel in a U format to reduce the overall length and to provide a mid-position measuring point. The heat exchanger is mounted on the H102 panel fascia and retained by locking pipe clips.
In normal operation, hot water from the heater and pump passes through the ‘HOT OUT’ braided hose and self-sealing coupling into the inner stainless steel tube. It then flows through the heat exchanger and leaves. Cold water flows from the ‘COLD OUT’ hose through the annulus between the clear plastic tube and the inner stainless steel tube. Six thermocouples measure hot and cold inlet, mid-point and exit temperatures.
The H102B Plate Heat exchanger is a 4-plate brazed model that demonstrates the basic principles of heat transfer. The heat exchanger is mounted on the H102 panel. Each plate is corrugated to promote turbulence and is perforated to allow the hot and cold streams to remain in sealed passages on opposite sides of the plates and allow the transfer of heat. It is the combination of turbulence, low volume, high surface area and high fluid velocities that give the high heat transfer capacity in a small volume.
Thermocouples measure the cold water inlet and return temperatures. The flow direction of the cold stream relative to the hot stream can be reversed by changing the location of cold inlet and exit tubes.
H102C – Shell & Tube Heat Exchanger
This miniature heat exchanger consists of a clear glass shell with end plates through which pass a bundle of seven equally spaced stainless steel tubes. Coupled to the end plates are end caps that allow hot water from the heater/circulator to pass through all seven tubes and then re-combine to return to the heater/circulator in a closed loop. Cold water from the mains supply passes through the clear glass outer shell and heat is transferred to this from the hot stream.
In normal operation hot water from the heater/circulator passes into the end cap via a stainless steel braided hose and self-sealing coupling. Its temperature at entry to the heat exchanger is measured by a thermocouple. It then flows through the seven heat exchanger tubes to the opposite end cap and leaves. Its temperature on exit is measured by a similar thermocouple.
H102D – Jacketed Vessel with Coil and Stirrer
The H102D Jacketed Vessel with Coil and Stirrer allows batch and flow processes to be examined with and without the use of a stirrer. In addition both jacket and coil heating methods may be investigated.
The vessel consists of a glass cylinder with annular jacket. Threaded hose connectors allow the jacket to be filled with hot fluid for indirect heating of the vessel contents. Alternatively, a glass coil submerged beneath the contents of the vessel may be used to indirectly heat the contents by passing hot fluid through the coil.
An adjustable overflow tube allows the level of the contents of the vessel to be controlled. The vessel contents may be operated in ‘Fixed Batch’ mode or ‘Flow Process’ mode. A height-adjustable thermocouple allows the temperature to be measured at any depth in the fluid batch and is connected to the panel indicator and the optional HC102 Data Acquisition upgrade (if available).
Flexible hoses allow the hot and cold streams from the H102 base unit to be coupled to the jacket, the coil and the vessel.
There we go – that’s our fab four. For completeness, the remaining seven in the range are:
H102E – Extended Concentric Tube Heat Exchanger
H102F – Extended Plate Heat Exchanger
H102G – Water/Water Turbulent Flow Heat Exchanger
H102H – Coiled Concentric Tube Heat Exchanger
H102K – Film and Dropwise Condensation
H102M – Water to Air Heat Exchanger Module
For full specifications on each, go to the product page and click the “Download Datasheet” button.
For more inquiries, please feel free to our technical specialist consultant in Civil:
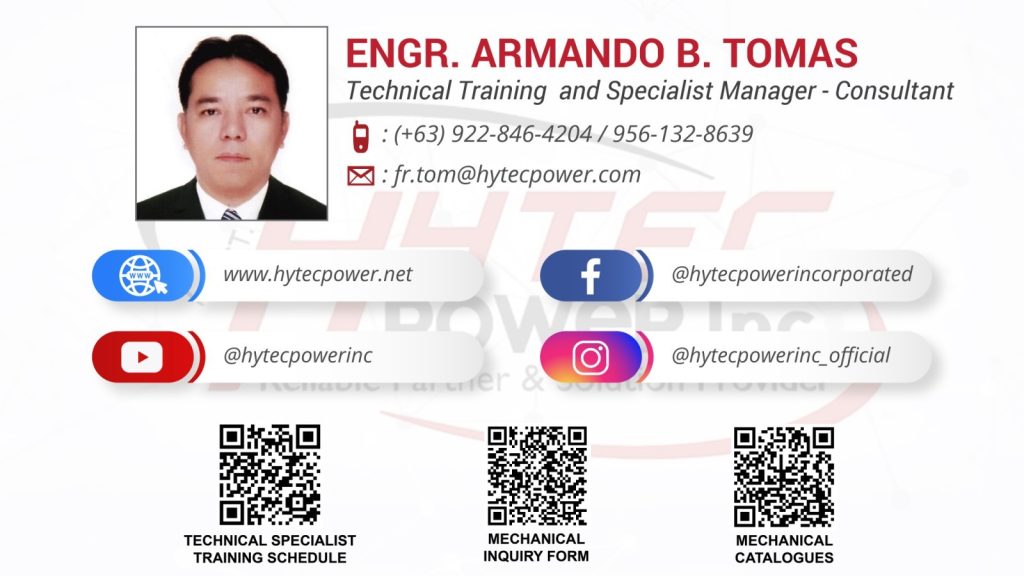