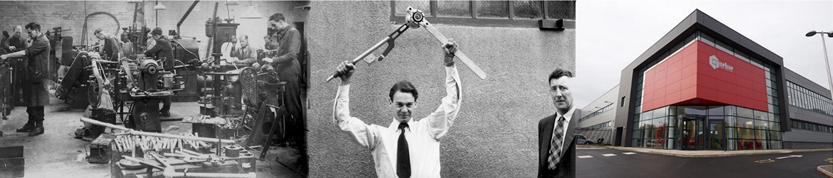
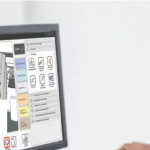
Neill Brodey is the managing director of Norbar Torque Tools and is the grandson of founder, Bill Brodey. Neill works at Norbar alongside his brother, Craig Brodey and cousin, Philip Brodey, all of whom are passionate about Norbar and manufacturing in the UK.
Neill sits on the International Standards Committee for ISO6789, the standard governing torque wrenches, and is President Elect of the European Hand tools Institute (CEO). He is also a regular contributor to the American Hand tools Institute (HTI), bringing a European perspective to their meetings.
Neill Brodey answers some frequently asked questions on the subject of torque tools, their calibration and torque tools in general.
Q&A TORQUE TOOLS AND TORQUE MEASUREMENT
Is it really necessary to use torque control, if we have always managed without it?
Yes, more than ever before. Whether you are manufacturing a product or maintaining one, there has never been more pressure to increase performance whilst at the same time, reduce cost and accurate torque control allows joints to be designed
more efficiently.
On top of this, the reliability and safety of your products will never have been under more scrutiny. Furthermore, you not only have to do the job right but you may be called upon to prove that you have done it right and your faith in your skilled workforce’s ‘feel’ for the bolt will not cut it in a product liability claim.
As with many other things, there is no substitute for using the correct tools, correct procedures and comprehensive documentation.
Isn’t it true that it is easy to over-torque with ‘click’ wrenches?
A clumsily used wrench will over-torque, despite the relaxation in the mechanism described above. Operators need to be trained in how to use torque wrenches correctly because it is possible to be both
quick and accurate with a click wrench. Wrench selection can also have a considerable bearing on the end result. Choosing a wrench that is comfortably long enough to apply the desired torque will not only enable the operator to use the wrench in a more controlled fashion but will reduce the strain on the operator and increase wrench life.
Wrenches described as ‘break back’ are designed to considerably increase the break angle of the torque wrench, extending the period after indication that the wrench is applying a reduced torque. The idea is that operators have a much longer time to check their momentum and avoid over torque.
There are also wrenches that slip at the desired torque. These wrenches remove the possibility of over torque but are mostly of a pre-set type, in other words, they don’t have a scale but are set to the desired torque against a torque tester. There is also
a practical limitation on the safe maximum torque of slipping wrenches to a little over 100 Nm.
The choice of torque wrench type is confusing. Should we be ‘upgrading’ to electronic, digital wrenches?
All of the types of torque wrench can be broadly categorized into two: setting wrenches and indicating wrenches. Setting wrenches are typified by the ‘click’ torque wrenches that most will be familiar with where you set the desired and the wrench will signal that it has reached this torque by a click torque or change in geometry.
Indicating wrenches will actually measure the applied torque by a mechanical analogue dial or electronic display. As a general rule of thumb, setting wrenches are used for assembly and indicating wrenches are used for quality control of already tightened bolts.
But isn’t it true that dial and electronic wrenches can be set to give an indication when they reach a predetermined torque so they can be used for both assembly and quality control?
True, the edges are becoming increasingly blurred between setting and indicating wrenches because most indicating wrenches can be set to bleep, illuminate LEDs or even vibrate at a pre-set torque. This along with accuracy claims well in excess of that claimed for click wrenches might lead you to believe that electronic is the way to go.
However, the click of a setting wrench is not just an audible and tactile signal; the wrench mechanism actually relaxes the applied torque for an instant. In this instant, the bolt stops rotating and to overcome static friction and re-start it requires more torque than was being applied at the moment of indication. The upshot of this is that a click wrench can be used with considerable speed compared with any indicating wrench, however insistent the electronic prompts to stop might become. When making an accuracy comparison between
electronic wrenches and mechanical setting wrenches, it is the actual result that you will achieve in real life situations complete with distractions and tight deadlines that really matters.
There is no question that indicating wrenches are superior in torque audit applications and, with care, can be used for assembly. Where the mechanical setting ‘click’ wrench has little answer is when you want to make a record, for statistical process control purposes, of all the tightening torques from your production line. Electronic wrenches can do this but be prepared to sacrifice some speed.
Do torque wrenches need to be wound back to zero after use?
If the wrench is wound back at all, it certainly should not be adjusted below the minimum scale marking (usually 20% of maximum) – never to zero. Beyond that, it really depends on the application. We have thousands of Production Type wrenches in service that are left at their setting for months on end without problem.
The occasional user should adjust back to the minimum scale setting after use. If you use the wrench in an environment such as a commercial garage, the choice is yours. Either way is acceptable.
What is Norbar’s place in the torque tool and torque measurement industry and how did the name come about?
Norbar is one of the foremost companies in the world dedicated to the field of torque tools, torque measurement and torque calibration. In 1942 our founders, Bill Brodey and Ernest Thornitt, responded to the Government’s plea to have torque wrenches manufactured in the UK. From these modest beginnings in North Bar Place Banbury, from which we derived our name, we have steadily grown to become an international company with full service subsidiaries on four continents and distributors in almost every country in the world.
Where can I learn more about torque control and the correct use of torque tools?
In this article we have barely been able to scratch the surface of a huge subject. There are of course many sources of reference but nearly 30,000 people have viewed Norbar’s ‘Best Practice’ videos on YouTube. We would also urge you to view Hytec Power Industrial department within www.hytecpower.com and http://ind-news.hytecpower.com/ where we have expanded on some of the subjects touched upon above.
For inquiries contact Hytec Power Inc. PH Distributor
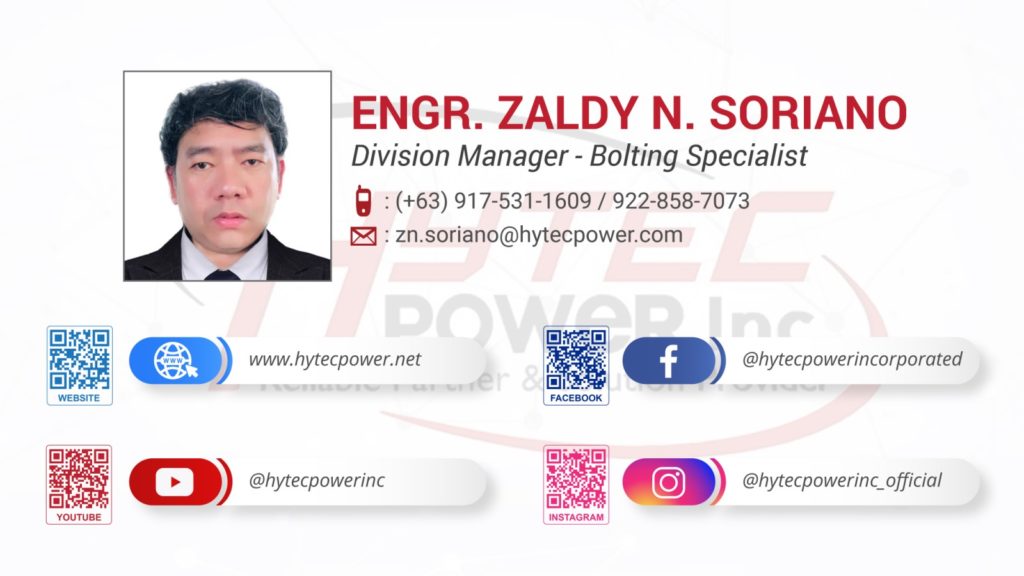