Currently, Actuator valves are used in many factories. They are used in wastewater treatment plants, power plants, oil refineries, mining and nuclear treatment plants, food plants and pipelines. process control automation. Automated valves vary in both design and size.
There are two main types of actuator valves: Electric actuator valve and Pneumatic actuator valve. We will learn about these two popular automatic control valves.
1. What is Actuator?
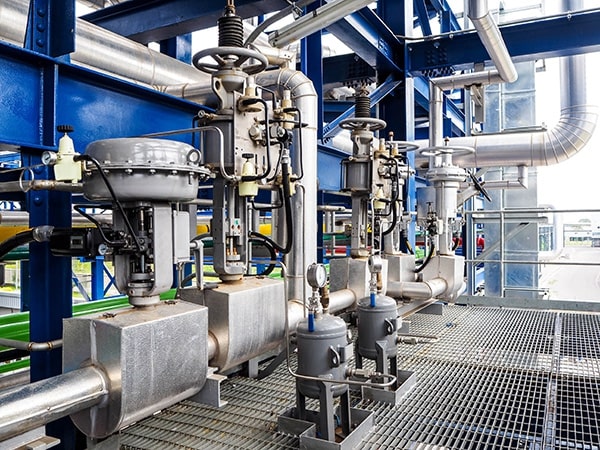
Actuator is a type of motor used to move or control a device or system. It is operated by power such as electric, pneumatic or hydraulic. convert that energy into kinetic energy to act on the system.
Actuator valve is an automatic control valve, this is a type of valve using electricity or using compressed air to control the valve to open / close by signal instead of manual operation.
Electric actuator is a device that uses electricity (24VDC, 220VAC, 380VAC…). While pneumatic actuator is an actuator operated by converting gas pressure into mechanical force to operate the valve.
2. Distinguishing Pneumatic Actuator and Electric Actuator
Electric Actuator
Electric actuator is an electrical controller, usually an electric motor, using common voltages such as 24V, 240V, 380V… When the control voltage is applied, the motor will move and control other devices according to the mechanism motion.
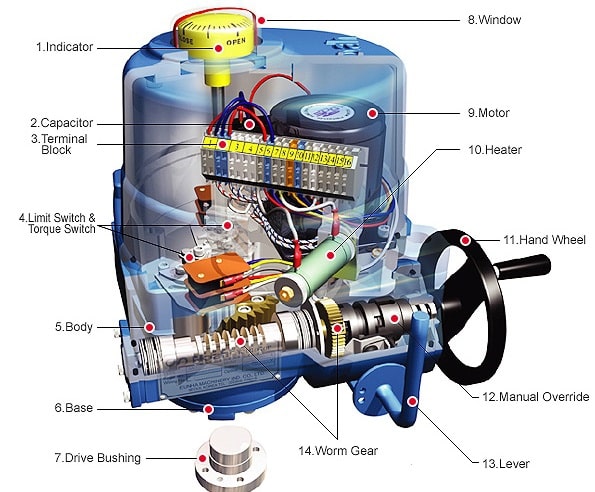
Electric actuator valve uses an electric actuator to control the valve to open and close automatically. Electric control valves use an electric motor to provide torque to operate the valve. They do not make noise, do not pollute the environment and save energy. However, the power supply must always be adequate.
The actuator can also control the opening and closing angle of the valve. This is a linear control line, it receives 4-20 mA control signal to adjust the rotation angle. This type of control is used in systems where precise flow control is required.
Some electric control valve lines are widely used such as:
Pneumatic Actuator
Pneumatic actuators convert energy from vacuum or compressed air at high pressure into linear or rotary motion. Compressed air is the ideal power source to drive a motor, because it can respond quickly to starting and shutting down.
Compressed air pressure is commonly used between 2 and 7 bar.
Single Acting Pneumatic (single acting set):
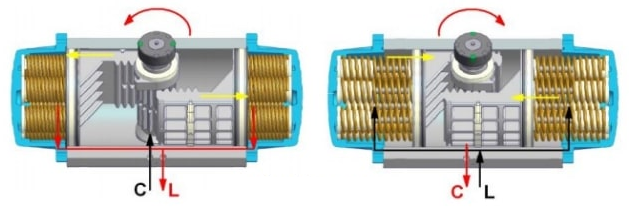
When supplying gas to the actuator to control the valve opening, the end of the gas supply process will automatically pull the slider in the actuator, followed by a rotating action to help the valve return to its initial state, normally closed or normally. open. This means that during operation, if the supply air is lost, the valve will return to the initial state of normally closed or normally open.
Double acting Pneumatic (double acting set):
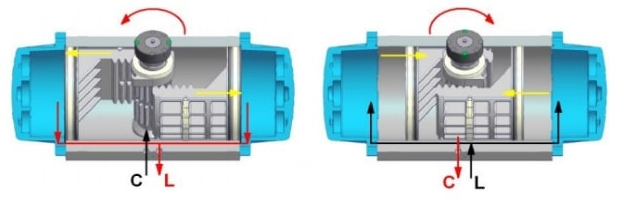
In the process of controlling the double-acting pneumatic actuator, in order for the valve to return to its original state, we must supply air to the actuator.
Some electric control valve lines are widely used such as:
Diaphragm Actuator:

The Diaphragm Actuator is used to precisely control and regulate fluid flow and pressure as required for fluid control in a wide variety of plant systems. These actuators are used for strong vapor, pneumatic action, not only for linear motion valves but also for rotary motion valves. It consists of 4 springs with high rigidity, capable of withstanding sudden changes in the dynamic force of the fluid acting on the valve body. Valve operation may be altered if the cap and 4 bolts are removed, the actuator is rotated excessively, and the cap is replaced.
Above, We have clearly explained about “What is Actuator”, “What is Electron Actuator”; and “What is Pneumatic actuator”. Hope this article can help you choose the optimal product line for your system. If you have any product needs, please contact us:
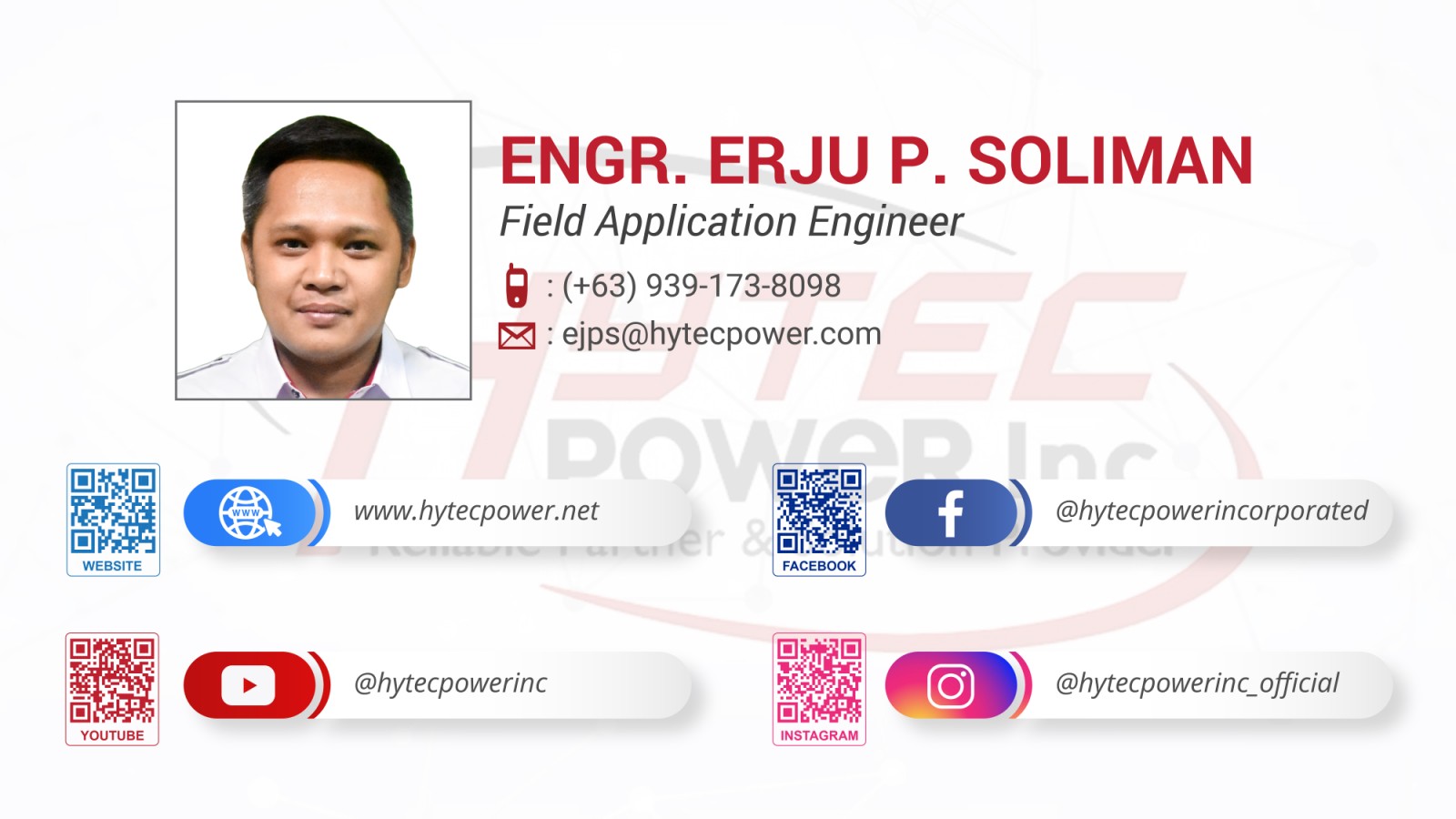
For more information visit: www.komoto.com.kr